May 3, 2019 | News & Events
Condexa Pro 500 Box, a pre-built floor-standing cabinet commercial boiler from Vokèra by Riello has provided a plug and play heating solution for a prestigious independent preparatory school in Berkshire. The fully modulating gas condensing boiler replaces an outdated oil-fired boiler and oil storage tank at the school and is installed externally, freeing up valuable internal space. Vokèra, through its parent company Riello Group, is a part of Carrier, a leading global provider of innovative heating, ventilating and air conditioning (HVAC), refrigeration, fire, security and building automation technologies.
With indoor space at a premium, the ability to install the Condexa Pro 500 Box boiler outside was a key benefit for the school, as was the compact footprint. The self-contained units are supplied with water and gas manifolds, flue exhaust duct and condensate evacuation line already fitted and connected. A water drain for each heating unit is also built in as standard. When required, an internal solution is also available.
In addition to its space-saving design, the Condexa Pro Box boiler offers exceptional efficiency versus return water temperature. Units incorporate a highly efficient heat engine, resulting in an extremely low return temperature/flue exhaust gas temperature (temperature differential). To assist specification, Vokèra’s technical team is able to calculate how much clients could save on their annual energy consumption by installing a Condexa Pro Box, based on their existing fuel tariffs. The boiler’s impressive energy efficiency is complemented by minimum polluting emissions due to the controlled pre-mix burner and micro-flame burner combination.
The Condexa Pro 500 Box boiler specified for the replacement project at the school features four heat exchangers in cascade configuration, offering 200kW total output. The innovative design enables easy access to all components from the front, and each combustion unit can be individually serviced and maintained without loss of other units, ensuring uninterrupted operation.
Condexa Pro Box fully modulating condensing boilers also boast the latest generation electronic control. Although the compact in-line solution installed at the Berkshire school is connected to an existing Building Management System (BMS), the boiler’s sophisticated heating control and monitoring may negate the need for a BMS in some applications. The advanced remote control facility allows a maximum distance of 100 meters and makes it possible for end-users to manage functions such as setting the boiler’s on and off timings and weekly programming of the circuit.

Apr 15, 2019 | News & Events
As the first anniversary of Boiler Plus approaches, Alister Maclachlan of Vokèra by Riello assesses the impact of this initiative and how the Government’s proposed policy review in April 2019 will be an opportunity to clarify some aspects of the legislation for installers and their customers.
Greater choice
Introduced in England by the Department for Business, Energy and Industrial Strategy (BEIS) in April 2018, Boiler Plus set new minimum performance standards for domestic gas boilers and made fitting timers and room thermostats a requirement to reduce energy costs for consumers. With the consumer at the heart of the legislation, Boiler Plus was designed to give people greater choice and more information about the products that are available to help them achieve optimum comfort and energy savings. But what’s the reality nearly one year on?
Although Gas Safe registered installers haven’t had to undertake any additional training to comply with Boiler Plus, it is obviously important that they understand the different options within the legislation in order to be able to advise their customers on the best solution for their particular needs. In this respect, Boiler Plus has placed greater responsibility on installers’ shoulders and so it is essential that they have the information they need regarding the benefits of each solution and the knowledge and skills to ensure best practice is followed.
Clearing the confusion
Going by the number of queries to our Technical Helpline since the new standards were introduced, there is some confusion surrounding certain aspects of the legislation. For example, an installer in the process of fitting one of our water heaters was asked by the householder if the unit complied with Boiler Plus. Unsure of the answer, the installer called our helpline and a member of our team was able to confirm that water heaters are outside the scope of Boiler Plus. Whilst it is unlikely that the legislation will be extended to cover water heaters, DHW demand does appear to be on the increase in many modern households. Delivering instantaneous hot water to multiple outlets at high flow rates, the latest high efficiency water heaters, such as Vokèra by Riello’s new AquaNova LE, can offer a reliable, energy saving domestic hot water supply for showers and other domestic applications.
Affordable option
Under Boiler Plus a new combination boiler must incorporate one of the following measures within the system:
- Flue Gas Heat Recovery (FGHRS).
- Weather Compensation.
- Load Compensation.
- Smart Controls featuring automation and optimisation functions.
I suppose it is inevitable that end-users and installers will be attracted to the measure that combines compliance with affordability, yet which still provides additional efficiencies without compromising comfort. Since Boiler Plus was introduced in April 2018 Vokèra has seen sales of external weather compensation sensors rise by approximately 60% compared with the same period in 2017. Clearly, this measure is regarded as a relatively low cost means of complying and the easiest to install compared with, say, smart controls or FGHRS. Perhaps it is not surprising that the FGHRS option is not proving particularly popular. These usually large, rather bulky units aren’t very attractive and there isn’t always enough space above the boiler to fit them.
Not so smart
Smart controls (complete with automation and optimisation) can provide an effective additional efficiency measure. However, some areas of the industry are calling for the definition of a smart thermostat within the context of Boiler Plus to be stipulated as an internet-connected device offering remote control of the heating system using a smartphone app, for example. Clarifying this in the forthcoming policy review would certainly distinguish a Boiler Plus compliant control from cheaper so-called ‘smart’ thermostats that are non-connected and which don’t offer consumers the same level of efficiency or convenience.
Whilst there are a number of compliant smart control solutions, it is worth looking for any additional features that will add to the usability of the control, ensuring the homeowner can make the most of their heating system, manage their energy efficiently and maximise comfort. The OpenTherm protocol RF control from Vokèra, for example, enables energy saving modularity and includes a handy ‘holiday’ function. Our BeSMART Wi-Fi enabled smart thermostat also offers full compliance and is very easy to install and intuitive to use. As an internet-connected device it allows homeowners to manage up to 8 different heating zones from anywhere in the world through the BeSMART App. In addition, a weather compensation function can be added that adjusts boiler output to reflect ambient temperature with no need to fit an external sensor. As a further benefit, BeSMART can alert customers (who have subscribed to remote monitoring) and the Vokèra Service Centre if something goes wrong, minimising disruption.
Positive change
We know change can be daunting and it can take time for industry to adjust, but we believe Boiler Plus should be seen as a positive change that will help tackle climate change and keep household energy costs down. At Vokèra we also welcome any initiative that steers installers towards fitting more advanced controls, thereby increasing their technical skills and bringing energy saving benefits to their customers. Nearly one year on, there are clearly some areas of Boiler Plus that could be improved – let’s just hope the distraction of Brexit doesn’t prevent the Government from addressing these issues and keeping its pledge to review this important legislation in April.
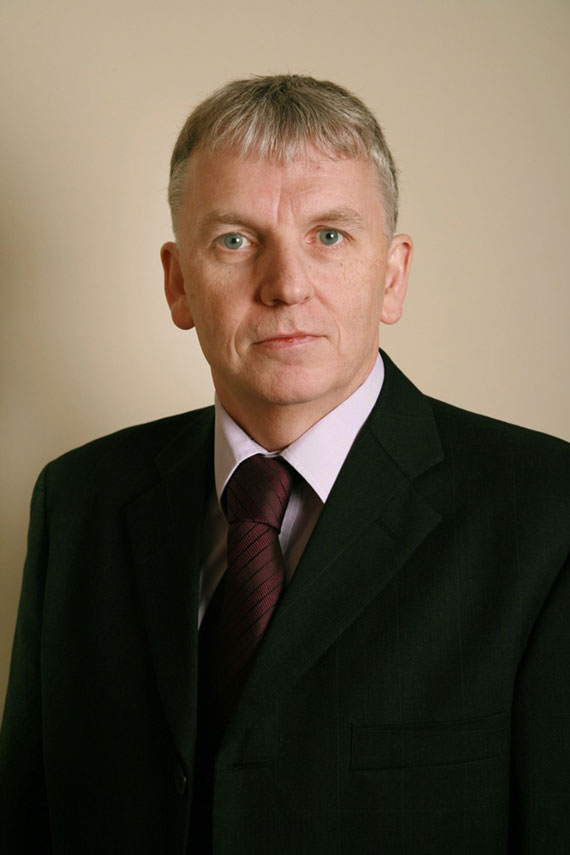
Mar 15, 2019 | News & Events
Space-saving design, system flexibility and advanced electronic control make Vokèra by Riello’s all-new Condexa Pro condensing boilers an ideal solution for a luxury hotel in Sheffield. The Best Western Plus Kenwood Hall has replaced six outdated boilers serving hotel rooms, kitchen, restaurant and public areas with three compact Condexa Pro 90 units. Vokèra, through its parent company Riello Group, is a part of Carrier, a leading global provider of innovative heating, ventilating and air conditioning (HVAC), refrigeration, fire, security and building automation technologies.
The new boilers are installed in a linear cascade configuration on a precision-engineered framework, purpose-designed to assist installation and allow easy access to all components from the front. In addition, logic integrated in the electronic control allows each boiler to operate either as a primary or a secondary in the cascade, ensuring constant operation, even while being serviced.
The Condexa Pro units replaced boilers that had become increasingly unreliable and inefficient. Sim Cowen, Managing Director, B P Dempsey Ltd, the local commercial heating specialists, recommended replacing them with Condexa Pro units.
“Cowen recommended Vokèra by Riello and his advice was spot on,” said Gary Dodd, Maintenance Manager at Kenwood Hall. “Our new Condexa Pro 90 boilers haven’t missed a beat since they were commissioned. In fact, they will probably be our preferred choice when the time comes to replace the remaining existing boilers at Kenwood Hall – and possibly across the group’s other hotels in the area,” he added.
Vokèra’s sales and technical team provided a comprehensive support package for the project, including a pre-sales report showing the proposed Condexa Pro 90 cascade configuration and how this would fit into the confined plant room space. Vokèra was also able to handle the requirement for an extended external flue to clear the roof of the hotel, which saved the cost of a specialist flue contractor.
“Kenwood Hall was my first Vokèra by Riello project but I’m sure it won’t be my last,” Cowen said. “The new Condexa Pro offers excellent value for money and it is designed to adapt to the most varied plant requirements. It’s also very compact and powerful, which meant that we were able to replace six old boilers with just three 90kW Condexa Pro which are more than able to meet the hotel’s heating needs in terms of output and efficiency.”
Vokèra by Riello’s new range of Condexa Pro wall-hung condensing boilers extend from 35 up to 131kW and offer solutions for new plants, replacements or renovations of old heating systems. Each versatile appliance forms the principle element in a system with almost limitless configurations, from simple standalone solutions to modular cascade systems, as at Kenwood Hall, that can accommodate specific requirements thanks to the wide range of accessories.
Among the most innovative components of the new Condexa Pro is an optimised stainless steel heat exchanger, designed and manufactured by Riello, with single or double coil patented sections and premix burners for high turndown ratio and low emissions. In addition, the calculation speed and advanced management algorithms of the electronic control system allow regulated ambient temperatures and the best possible operation performance both for standalone boilers and for multiple cascades up to 10 units.
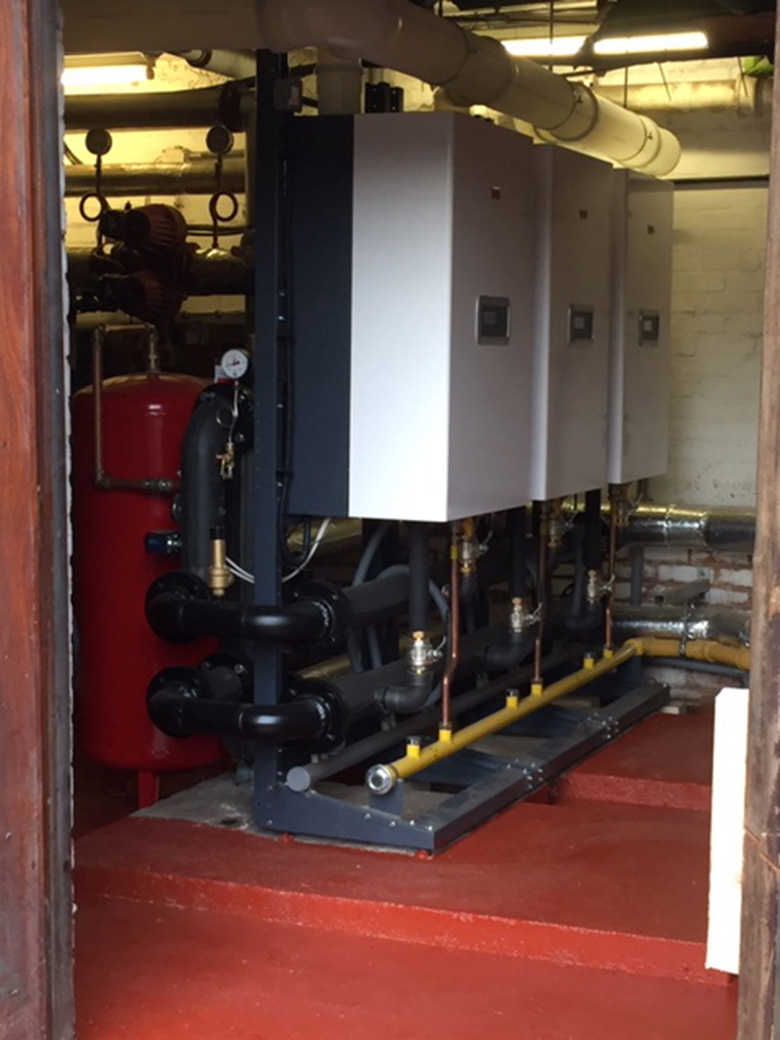
Feb 7, 2019 | News & Events
John Smith, National Service Manager UK at Vokèra by Riello, offers advice on keeping condensing boilers running reliably and efficiently during a winter freeze.
Whilst it may be too early to predict whether the UK will suffer another ‘Beast from the East’ this winter, it is always better to be prepared for whatever the weather has in store. As any installer will know, when the temperature drops and central heating thermostats are ‘turned up’ the number of calls to fix ‘broken’ boilers goes up too. Whilst modern boilers are designed and tested to deliver optimum quality and reliability they still have moving parts that can be affected by general wear and tear, as well as parts that have a natural lifespan and need to be replaced. However, ensuring that an inconvenient and potentially costly breakdown doesn’t happen when the appliance is most needed could be avoided.
Getting a gas boiler serviced on an annual basis by a Gas Safe registered engineer is key to ensuring a boiler won’t let the homeowner down when the cold weather arrives and please remember to follow the manufacturer’s instructions. For example, on sealed system boilers it is important to check that the system water pressure is correct as it may have dropped while the heating has been idle during the summer months. The expansion vessel also needs to be sufficiently charged and radiators may require bleeding, however remember to top up the system water pressure after. The heating system is tested to ensure it is operating correctly and should any problems be found these can be dealt with ensuring that the homeowner stays warm during the colder months.
Frozen condensate
When servicing high efficiency condensing boilers, now widely installed in UK households, condensate traps should be checked and cleaned where necessary for any combustion debris as this can lead to blockages, which will eventually cause the appliance to malfunction.
Prolonged periods of extremely cold weather can create another problem in this part of the boiler – frozen condensate. This happens when the condensate discharge pipe on the boiler freezes and becomes blocked with ice, eventually causing the boiler to shut down. This was an all too common reason for calls to boiler service companies during the severe winter in early 2018. So how can installers minimise the risk of freezing and keep their customers’ condensing boilers running whatever the weather?
Golden rules
A correctly installed and commissioned condensing boiler will extract latent heat from the flue gases and produce condensate, which must then be removed from the boiler. Building Regulations advise the correct way of terminating condensate discharge pipes and currently allow these to be run either internally or externally or a combination of both. A boiler shutdown due to a blockage caused by frozen condensate usually occurs when the pipe has been installed externally for some of its length and is, therefore, exposed to very low temperatures. A guide for installers to prevent frozen condensate in discharge pipes has been published by the Heating & Hotwater Industry Council (HHIC), stresses the importance of adhering to relevant standards and the appliance manufacturer’s instructions. Vokèra fully supports HHIC in its efforts to promote best practice among heating installers and by following ‘Golden Rules’ to avoid a frozen condensate.
1. Disposal method
Where possible, an internal condensate disposal method should always be the preferred option to keep pipework within the thermal envelope of the building. However, it should be noted that installing in unheated ‘indoor’ locations, such as a loft or garage, should be considered as ‘external’.
2. Pipe runs
External runs should be as short as possible, preferably no longer than 3 metres. Also, any external boiler condensate pipe must be a minimum internal diameter (ID) of 30mm, and insulated using suitable waterproof and weatherproof insulation.
Any internal condensate pipe should be a minimum of 19mm ID and upsized to 30mm minimum ID before passing through the building structure to the outside.
3. Adequate fall
Providing adequate fall is a critical factor as this allows the condensate to drain away correctly from the boiler under gravity and so prevents it from collecting in the pipe and freezing in winter. Vokèra recommends a minimum 3 degree fall, with bends and fittings kept to a minimum. It is also worth mentioning that this minimum drop must be maintained from the boiler right through to the discharge point.
4. Above the line
Where condensate pipework terminates externally to an outside gulley or drain, the pipe must terminate above the water line, but below the grate by at least 25mm, with the end cut at a 45 degree angle. A drain-guard should also be fitted: these steps help to minimise the risk of blockage or freezing through wind chill.
5. Checklist
Details of the condensate drainage installation should be recorded as part of the Benchmark Commissioning Checklist, a nationally recognised scheme managed by HHIC.
6. Electric Trace heating
Where an external condensate discharge pipe is installed, the customer should be made aware of the risks and consequences of its freezing and can be offered the option to fit trace heating (or other measures approved by the boiler manufacturer or service company) but must follow installation instructions of the trace heating manufacturer.
Promoting Best Practice
According to a report by the HHIC, during the peak of the extreme weather experienced in early 2018, the UK’s gas emergency number control room took over 40,000 calls from members of the public. It is interesting to note that the vast majority of these calls were not boiler fail emergencies but people seeking help because their gas boiler had stopped working due to the condensate pipe becoming frozen.
We have to accept that there are circumstances in which there is no other option but to install condensate discharge pipework externally and as a result that pipework will be at risk of freezing in extreme weather conditions, particularly when there is a high wind chill factor. It is therefore vital for installers to follow manufacturer’s instructions and current regulations/standards to minimise this risk. For its part as a leading boiler manufacturer, Vokèra will continue to work with industry bodies like HHIC to emphasise the importance of correct condensate discharge installation and to improve compliance through product innovation, training, and good practice guides.
Jan 15, 2019 | News & Events
If you thought combination gas boilers were only suitable for smaller homes, then think again. Alister Maclachlan, product director of Vokèra by Riello, explains how the latest high output appliances can meet the higher demand for heating and hot water in larger properties as well as those homes with multiple outlets.
When choosing a combi gas boiler that best fits the needs of a property and its occupants it’s not all about the size of the dwelling. For example, an older, four-bedroom house with one main bathroom and just two occupants may not use as much hot water as, say, a family living in a modern semi-detached that has an en-suite, family bathroom and downstairs cloakroom. The bedroom-bathroom ratio has certainly increased in recent years, particularly among new homes. Once seen as something of a luxury in bigger properties, the en-suite bathroom can now be a standard feature in an average-sized new build.
Instant appeal
It is quite common in the UK for domestic hot water to be produced ‘instantaneously’ in a combination boiler. Water is heated on demand as an alternative to using a lower powered boiler that heats domestic hot water over a period of time in a separate thermostatically controlled insulated storage cylinder. As combi boilers don’t require external hot water cylinders or water storage tanks they offer savings in space and installation time, which brings advantages for users and installers alike. And because hot water is only produced when it is needed, having a combi also helps conserve water in the home in accordance with Building Regulations relating to water efficiency. With all these benefits it’s not surprising that this option now represents around 80% of the UK’s domestic boiler market.
Innovative alternative
A combi boiler is designed to provide hot water ‘on tap’ so to speak. When this innovative alternative to the traditional gas boiler first came onto the market around 30 years ago there was a common assumption that the typical output and flow rate of this type of appliance were best suited to smaller homes. This came about, in part, because traditional boilers tended to be sized in accordance with the number of radiators and capacity of the hot water cylinder. So when a homeowner decided to replace their old boiler with a new combi the installer would most likely fit one with the same output, when in fact a higher output was needed to achieve the desired flow rate.
Of course, there wasn’t such a wide choice of outputs available in those early days. This is no longer a problem as most of today’s manufacturers offer high output combination boilers. Vokèra’s evolve 42C, for example, is a 42kW combi with flow rates of over 17 litres per minute at a 35°C temperature rise. It has been specifically developed to provide comfortable, affordable heating and on-demand hot water in larger homes. It can also provide an energy efficient solution for properties with larger central heating requirements and multiple bathrooms.
Ask questions
As already mentioned, specifying the right combi boiler is not simply down to the actual size of a property. More importantly are the number of outlets and the occupants’ expectations when it comes to their heating and hot water supply. In order to understand the latter the installer would be well advised to ask the customer a few lifestyle questions, such as do they prefer baths or showers – or maybe both? And are they likely to want to run two showers simultaneously, or a bath and a shower at the same time? Their answers will indicate the output and flow rates required, enabling the installer to size the boiler accordingly. Another important factor is the likely inlet temperature. This can vary by several degrees across the UK, from the typically colder north to the warmer south, and that difference needs to be taken into consideration when specifying the boiler.
Modulation ratio
When selecting a combi boiler it is also crucial to consider modulation ratios and to remember that performance isn’t just about kW output. Installing a combi boiler with a high maximum output and a wide modulation ratio will deliver optimal efficiency and comfort. A good modulation ratio reduces constant on/off cycling, improving efficiency and boiler longevity. If a boiler has a high maximum output – let’s say 40kW – yet only has a modulation ratio of 4:1 it will only be able to modulate down to 10kW. However, when most rooms have reached the required temperature and radiator TRVs have closed, the demand on the boiler will be considerably less than 10kW. This means that the minimum output of the boiler will be higher than it needs to be, so the boiler will constantly switch on and off, leading to fuel inefficiency. This will also place unnecessary stress on the boiler’s components and parts. A boiler with a high maximum output and a wide modulation ratio, however, will be able to modulate down to an extremely low output, reducing wear and tear on primary components (fewer on/off cycles increase component longevity) and optimising fuel efficiency.
Also, a poor modulation ratio can be a particular problem for combis as it means they will be unable to maintain a stable domestic hot water (DHW) flow temperature at a low flow rate, and might even cause the burner to switch off during operation. This can be a significant issue for end users who prefer showers rather than baths. It is also an important consideration for households that require a constant DHW outlet temperature, such as where there are young children or elderly people who may be at a higher risk of scalding.
The combination gas boiler has certainly come a long way in the last couple of decades and new high efficiency, high output models have busted those outdated myths about poor flow rates. Correctly specified and installed, a modern combi will meet the needs of even the most demanding household in virtually any size property.
Dec 12, 2018 | News & Events
Bournemouth-based Absolute Plumbing Services recently completed a major home heating system upgrade for a residential customer using Vokèra by Riello’s new high-performing evolve boiler. Installed in combination with its BeSMART control system, the new system represents a significant improvement for the homeowner that will deliver substantial performance, efficiency and ease of use benefits.
The key driver behind this new installation for the three-bedroom, one-bathroom property in Bournemouth was the failure of the existing back boiler that had served the home for more than 40 years. Absolute Plumbing Services recommended a complete overhaul of the gravity fed system that included disconnecting the back-boiler unit, pump, controls and tanks in the loft along with the removal of the existing hot water cylinder. Original galvanised pipework and out of date radiators would also be removed and replaced. A Vokèra by Riello evolve, operating on a pressurised system with a BeSMART controller, provided the perfect, simple to operate boiler replacement solution.
Darren Rice of Absolute Plumbing Services takes up the story. “With the back boiler clearly beyond repair, this was the right time to review how and where we could make improvements for the homeowner. Our primary focus was to take advantage of the latest, most fuel-efficient technology to reduce running costs. Using an evolve combi, together with a BeSMART control, ensured we could deliver on those promises, and more.”
The evolve is a cutting-edge range of combi and system boilers capable of meeting a wide variety of applications. The 32C model installed in this project offers an A-rated space heating efficiency of 94 percent under the Energy-related Products (ErP) Directive. By adding Vokèra’s BeSMART internet-connected thermostat to the system with weather compensation enabled, the solution is rated an A+ heating package under ErP. As the OpenTherm protocol is embedded in the evolve range, BeSMART acts as a Class VI control, improving the heating system efficiency by 4 percent. This control solution also complies with the new Boiler Plus legislation that came into force in England in April 2018.
The boiler also provides a ‘comparative hot water efficiency’ of 77 percent under the UK Building Regulations’ Standard Assessment Procedure. It will condense in domestic hot water mode thanks to its next generation plate heat exchanger and provides class leading domestic hot water flow rates into the house.
Specifically designed to be quick and easy for installers to fit and service, the evolve helped Rice and his team complete this renovation project within just five days. With no available room for the boiler in the compact kitchen, they located the evolve in an adjacent space, with a right-hand side flue option. The boiler’s pre-fixing jig, complete with its built-in filling loop, saved important time in running and connecting new pipework and installation while integral frost protection made possible its location in an unheated space.
The REC10 liquid crystal display user interface saved set up and commissioning time. The full text menu-driven control helped Darren quickly navigate through evolve’s parameters and settings.
“This is the first time I’ve fitted an evolve unit and I was very impressed. It’s a well-designed, good-looking and extremely efficient boiler, even more so when you add the BeSMART control. Along with the other improvements, we’ve made to the system, the homeowner will save energy, enjoy better water flow rates from a pressurised system and there’s no risk of water leakage from the old tanks in the loft. BeSMART makes control of the system much easier too – even allowing remote control of the heating over Wi-Fi for extra convenience.”
The evolve also displays system pressure which can be monitored remotely via the BeSMART. As an added safety feature, the boiler incorporates a carbon monoxide (CO) monitor and alarm, which checks the level of CO and will shut off the boiler if excessive CO is emitted.
This installation is covered by a 10-year warranty available on evolve boilers when fitted with BeSMART and registered via the Vokèra Affinity loyalty and reward programme. More details on evolve and its accessories can be found here: http://www.vokera.co.uk/evolve/.
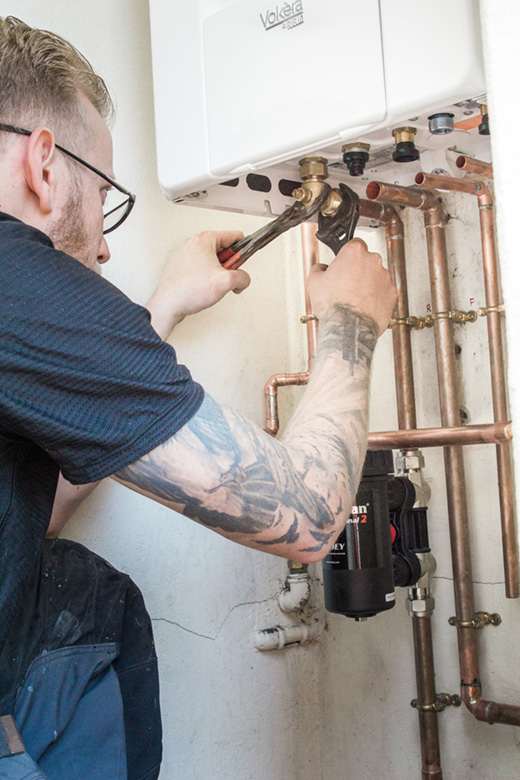
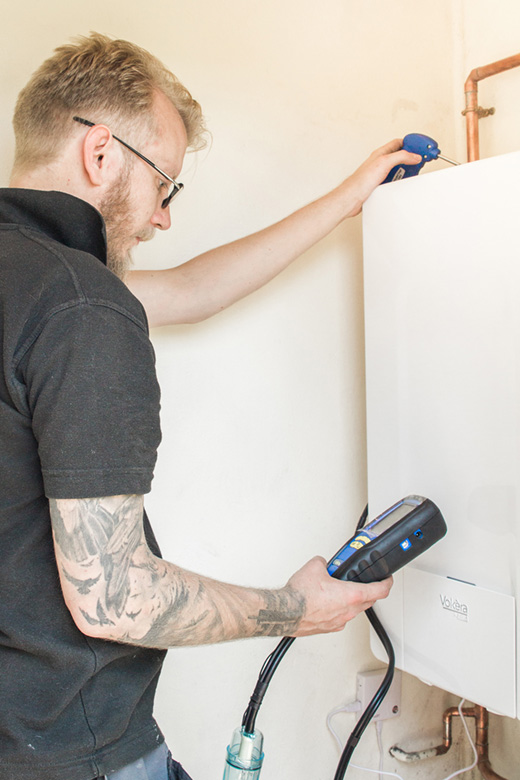
Oct 12, 2018 | News & Events
CALLAN, Ireland, 12 October 2018 Vokèra Ireland, is celebrating 20 successful years of supplying commercial and domestic boilers across Ireland. Today, Vokèra by Riello is one of the country’s best-known brands with more than 100,000 boilers installed throughout Ireland. Vokèra is a subsidiary of Riello Group, which is a part of UTC Climate, Controls & Security, a unit of United Technologies Corp. (NYSE: UTX).
Marking this milestone, Managing Director of Vokèra Ireland, Neil Gaffney, says the company is unique in the Irish market because it is the only boiler manufacturer subsidiary that offers the full range of functions – from installation training to call-centre support and after-sales service. “We work hard to ensure that we deliver the best quality products supported by dedicated, knowledgeable staff.” he says.
Originally started when the company’s Irish sales distributor convinced them to set up a dedicated Ireland division in 1988, the business became an official part of Vokèra in 1998. At that time it had just three employees who were based at a facility in Callan, Co. Kilkenny. The Callan facility now handles all installation, customer service and ongoing service requirements with a staff of 16 who are dedicated to helping installers, specifiers and end-customers. Vokèra Ireland employs six full-time engineers: one in Belfast and five in Eire who cover the whole of the island – the only company in the country that has this capability.
The business has certainly had to pull through some tough times during the past 20 years. In 2010, Ireland experienced a severe recession. “The recession was a huge challenge for us,” says Gaffney. “We had ridden the economic boom in Ireland, growing the business significantly on the back of all the new residential developments. When the recession hit, that work disappeared almost overnight and we needed to replace it quickly. We started to concentrate on retro-fitting and boiler replacement, and managed to grow this area of business.”
As for the next few years, Gaffney is optimistic about the company’s future. “The Irish economy is still buoyant,” he says. “The country needs to build at least 50,000 new homes in the next three years, and we would expect to be able to provide a significant percentage of the heating requirements for those homes.” Vokèra Ireland also expects to grow the commercial heating side of the business as it rolls out a new range of boilers, which are ideal for hospitals, schools, care homes and other businesses. “And we’re excited about renewables too,” continues Gaffney. “We have launched a heat pump and solar thermal products, which help to generate cleaner energy – and we believe this is going to be an exciting market for the future.”
Plans to celebrate the 20th anniversary are well under way, with a grand event in December. The opening of the current Vokèra Ireland site in 1998 featured a live band, Irish dancers and a wide range of the company’s customers at the time, and Vokèra Ireland expects to have just as much fun two decades on.
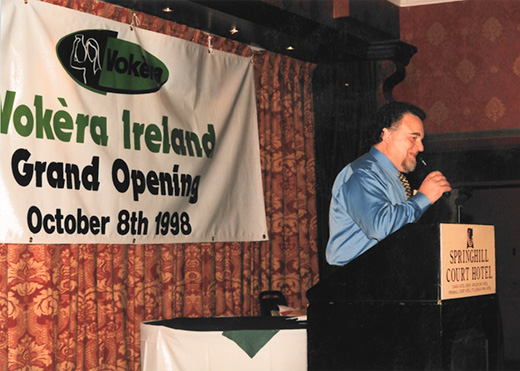
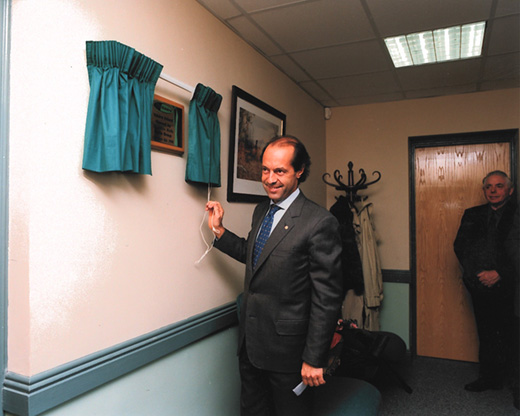
Sep 19, 2018 | News & Events
High standards of quality and reliability are vital in the development and manufacture of today’s high efficiency boilers for commercial and domestic applications. Alister Maclachlan, Product Director at Vokèra by Riello, looks at the five key stages of quality testing in the journey from product concept through to market launch and beyond.
1. Research and development
Technology is constantly innovating and evolving all around us and the heating industry is no exception. As a result of significant investment in research and development by manufacturers, modern gas boilers are more reliable than they’ve ever been. Now accounting for around 80% of the domestic boiler market the combination boiler, for example, has come a long way since it was first launched in the UK over 30 years ago. The perceived vulnerabilities in earlier generations of this popular appliance were addressed through intense quality testing of individual components and overall design. And it is this commitment to optimum quality and reliability that has given manufacturers the confidence to offer much longer warranties on their products, which is great news for installers and their customers. For example, a free 10-year warranty is now available on selected Vokèra boilers installed with our BeSMART Wi-Fi enabled thermostat. This is a major advance in the boiler market, particularly when you think that the average life expectancy of a traditional gas boiler was generally considered to be between 12 and 15 years, subject to the appliance being well maintained and serviced annually.
2. Accelerated life testing
Introducing the innovation and style the market demands, without compromising quality and reliability, can be a challenge for boiler manufacturers. Needless to say, the solution to this comes back to testing and more testing. Every component is thoroughly tested under laboratory conditions before it can be considered for use in one of Vokèra’s new products or as an upgrade to an existing appliance. Typically, components will undergo MTBF (Mean Time Between Failures) testing and accelerated life testing. MTBF is a method of testing large quantities of components for a specific period, let’s say 100 components for 1,000 hours, in order to calculate the failure rate over a longer period, for example, 1 million hours. Only when these tests have been completed to the R&D team’s satisfaction can a product progress to the next stage – extensive field trials. These trials are designed to see how the appliance performs in real-life conditions. Ideally, field trial boilers should be installed where they will be subjected to normal or even adverse operating conditions. Only when these trials have proved successful can the move to mass production be considered.
3. Batch testing
During assembly, further inspections are conducted and settings such as combustion readings are checked. After assembly each appliance is subjected to what is generally referred to as the ‘final test’. At Vokèra we also undertake batch testing at this stage, which means taking 2% of these appliances for stringent retesting lasting around two hours per appliance. An additional 0.5% of all appliances are then selected for further rigorous testing in our laboratory which takes a minimum of 12 hours per appliance. This ‘drill down’ quality test ensures that our ‘final test’ procedure is reliable and also acts as an early warning of any potential component batch issue.
This intense level of testing helps to ensure that ‘out-of-the-box’ reliability is consistently high. And we believe it is important to continue component testing to maintain, or even improve, product reliability in the field, particularly in the light of today’s longer warranties. Reporting systems enable our engineers to fast track any quality issue they encounter directly to the quality department via their PDA in real time. If required, corrective action can then be carried out quickly, minimising any potential impact or inconvenience to customers.
4. Lifetime reliability
Feedback from the field is invaluable for monitoring the inherent quality and reliability of products and individual components not only during an appliance’s warranty period but also throughout its lifetime. The Weibull or ‘bathtub’ curve is an established engineering model for plotting component reliability during a three-part timeline. This starts with a decreasing failure rate known as “early failures’, through to the relatively low failure rate of “normal or useful lifetime”, and thirdly the increasing failure rate at the “end-of-life” phase. Together, these three segments look like a bathtub with two steep edges and a flat bottom – hence the name. Indeed, we have used this model to identify key areas where action can be taken to extend product reliability periods.
5. Improvement strategies
Many modern manufacturing environments have adopted recognised techniques and tools to improve quality and productivity in all areas of the production process. Among these is Kaizen, a Japanese concept meaning ‘improvement’, which we have deployed in our state-of-the-art manufacturing facilities. Kaizen involves employees at all levels working together proactively to achieve regular, incremental improvements to the manufacturing process. It embodies positive strategies for productivity improvement, total quality culture and zero defects. The widely used ‘Just In Time’ practice is part of Kaizen and is proven to bring benefits to all types of process including shortened lead times and reduced inventory. In addition to Kaizen, Vokèra uses Six Sigma – first developed at Motorola in the 1980s as a method to improve process quality and reduce variability – the enemy in every aspect of business. By decreasing process variation companies can achieve defect reduction which, in turn, will lead to improvements in product quality, customer satisfaction, profits and employee morale.
When an appliance leaves the factory we don’t know who will install it, where it will be sited, or to what type of heating system it will be connected. With so many unknowns and variables, a commitment to upholding the quality and reliability of each and every product is paramount. Extensive testing before an appliance gets to market, and continuous performance monitoring when it does, helps to ensure a successful, and most importantly, safe installation every time.
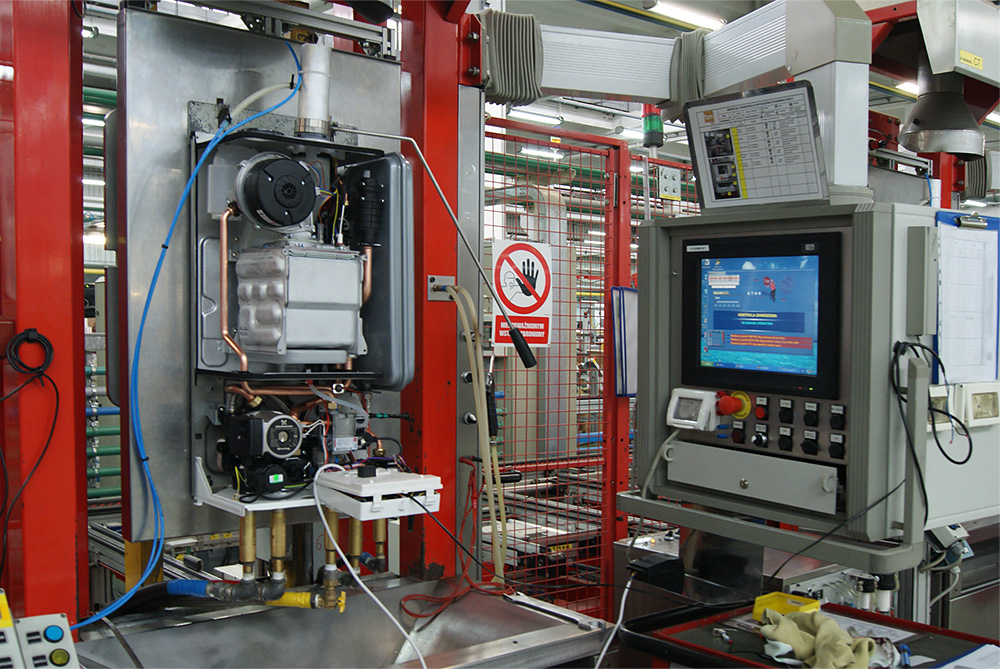
Aug 30, 2018 | News & Events
Getting a gas boiler inspected on an annual basis by a Gas Safe registered engineer is key to maintaining boiler efficiency, reliability and, most importantly, safety. But we often get asked what is the difference between a boiler ‘safety check’ and a ‘service’? Darren Payne, operations director at Vokèra by Riello, offers his thoughts on the differences.
When it comes to booking a boiler service we know that some consumers will be driven purely by price and choose the cheapest options available without fully understanding what will and won’t be covered during the engineer’s visit. However, not knowing the difference between a service and a safety check could prove to be a false economy and may even invalidate any manufacturer’s warranty. That’s why we always advise engineers to make the differences clear to their customers. Let’s start by looking at the basic checks to ensure the safety of the user and the appliance.
Safety check
First and foremost, always start by asking the customer whether they have had any issues since your last visit, as much can be gleamed in a five minute conversation with the customer before you put your toolbox down.
- Visual inspection of appliance and entire flue system to ensure there are no signs of distress and installed as per manufacturer’s instructions.
- Flue gas analysis (room sealed boiler) to verify combustion characteristics; including but not limited to leaks within flue system and adequate supply of air for combustion.
- Check ventilation is adequate for appliance type and/or location.
- Gas rate check to ensure adequate fuel supply with inlet working pressure and burner pressure as necessary.
- If a sealed system, relieve pressure in the water circuit and check expansion vessel pressure is correctly charged.
- Refill a sealed system to the correct operating pressure and disconnect the filling loop or link. (Permanent connection to class one potable water without fitting a specialist valve can be subject to a fine).
- On an open vented system, locate the feed and expansion cistern to check the ball valve is operating correctly, that there is sufficient water in the cistern and that gaps between water level, overflow outlet and ball valve outlet are correct (these provide the expansion space and backflow prevention). Also ensure Open Vent Pipe is free to discharge back into the tank.
- Ensure the condensate outlet(s) from the flue or heat exchanger are clear, free running, with sufficient fall (Vokèra recommends at least 3°) and terminated correctly.
- Visually inspect the condensate trap, but preferably dismantle, clean, refill and complete an operational check.
- Remove combustion box or cover to inspect seals on internal automatic air vents and check for evidence of any leaks.
- If a sealed system, check any pressure relief devices for signs of leakage or malfunction.
- Check operation of all safety devices to ensure they are working as intended.
Annual service
In addition to these safety checks, manufacturer’s instructions may also include
- Removal of burner door / cover and physical cleaning of heat exchanger flueways, inspection of flame rectification probes, spark gap etc.
- If appliance has a separate secondary heat exchanger, remove access cover and clean inside.
- Inspect insulation panels / shields.
- Replace door seals as required by manufacturer when reassembling.
- Check dilution levels of inhibitor and top-up if deemed necessary.
- Bleed any vent points around the system.
- Record Service Intervention in Benchmark Log, typically located in back of manufactures instruction booklet.
Integrated service reminder
By adhering to the manufacturer’s instructions, the appliance can be maintained in good order and used safely. Additionally, most current Vokèra boilers include an integrated service reminder/timer based upon the boiler’s true condensing operation that will alert the user or engineer whether a full service is required (the boiler operates as normal but the display or status LEDs will remain illuminated to draw attention to the fact in a manner similar to that in a modern car).
Don’t wait until winter
And while we are on the subject of service reminders, It’s worth mentioning the benefits of encouraging homeowners to book a service before the winter, rather than leaving it until the cold weather starts to bite and then discovering their boiler isn’t working as well as it should. A summer service will uncover any technical faults that need fixing to be sure of a warm home come the winter
Simplifying servicing and repairs
Through the development of smart heating controls, such as Vokèra’s BeSMART, servicing is also becoming a much easier process for installers, homeowners and landlords. For example, when a compatible Vokèra boiler is connected to BeSMART, the intelligent control system will alert the homeowner if a fault is detected. And with permission from the customer, installers can also gain access to a protected technical menu of which offers them information and the ability to adjust parameters where necessary. This development makes some of the elements of servicing and repairs a far simpler, quicker and smoother process for all.
Jul 31, 2018 | News & Events
Neil Mattock, marketing director at Vokèra by Riello, considers a recent study that reveals how installing a new boiler will net the biggest profits when it comes to selling a property.
When people are considering making renovations to their home the thought of adding value to the property can be an important factor. However, experts have found that while most improvements will increase the potential asking price, the added value is not always greater than what was spent in the first place. The insurance comparison website, GoCompare, teamed up with property expert Henry Pryor, to identify the upgrades that are really worth the money – and you may find the results surprising.
According to the experts, the most profitable home improvement is installing a new boiler for a cost of less than £2,000, which is estimated to add £8,000 in value, making a profit of £6,000. In contrast, the study found that updating kitchens and bathrooms is unlikely to add more value than the cost involved. For example, at an average cost of £7,000 a new kitchen will add £4,000 in value, while spending £4,250 on a new bathroom will add just £2,000.
Investing in a new boiler is clearly a good investment and homeowners can maximise that investment by choosing a boiler that combines industry-leading efficiency and ease of installation with a highly competitive product warranty. With all these requirements in mind, Vokèra’s evolve range of A-rated combi and system boilers feature a space heating efficiency of 94% under the Energy-related Products (ErP) Directive. The majority of Vokèra’s domestic gas boilers also come pre-configured for load and/or weather compensation via the OpenTherm protocol, so also easily comply with the recent ‘Boiler Plus’ legislation.
On top of this, evolve comes with a 7 years out of the box warranty, which is upgraded to 10 years with a Vokèra BeSMART (Internet connected) thermostat installed and the installation registered via Vokèra Affinity installer loyalty and reward programme. Also, by including BeSMART, the system becomes an A+ heating package under ErP – adding even more value to the installation. As well as giving end-users more control of their heating from anywhere at any time via the dedicated App, BeSMART provides installers with access to a protected technical menu, enabling them to adjust the boiler parameters.
With energy prices always on the rise, improving the green credentials of a house to make it more energy efficient will make it more attractive to potential buyers. So perhaps it is not so surprising that fitting a new high efficiency boiler is rated among the best value home improvements that will deliver the benefits of warmth, comfort and long-term performance to a property’s current and future owners.
To find out more about this, and other relevant subjects take a look at Vokèra’s YouTube channel.
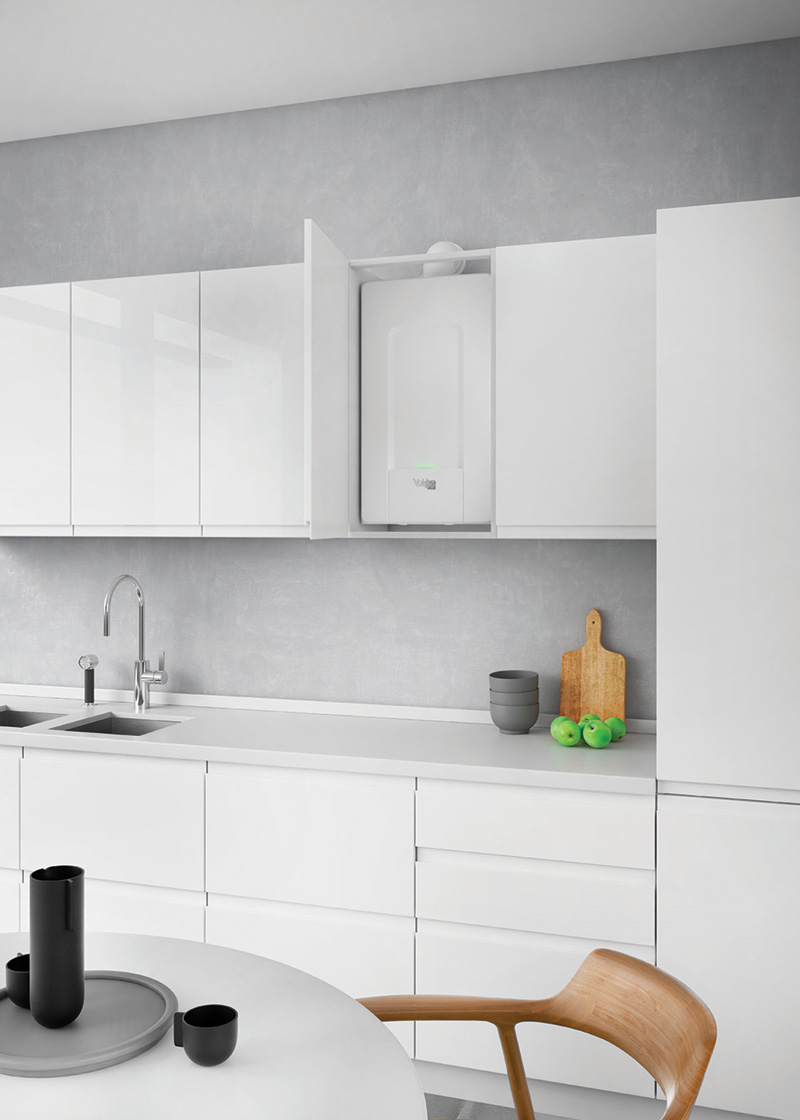